«Сплав» продемонстрирует на выставке «ЭкспоЭлектроника» гибкий печатный кабель
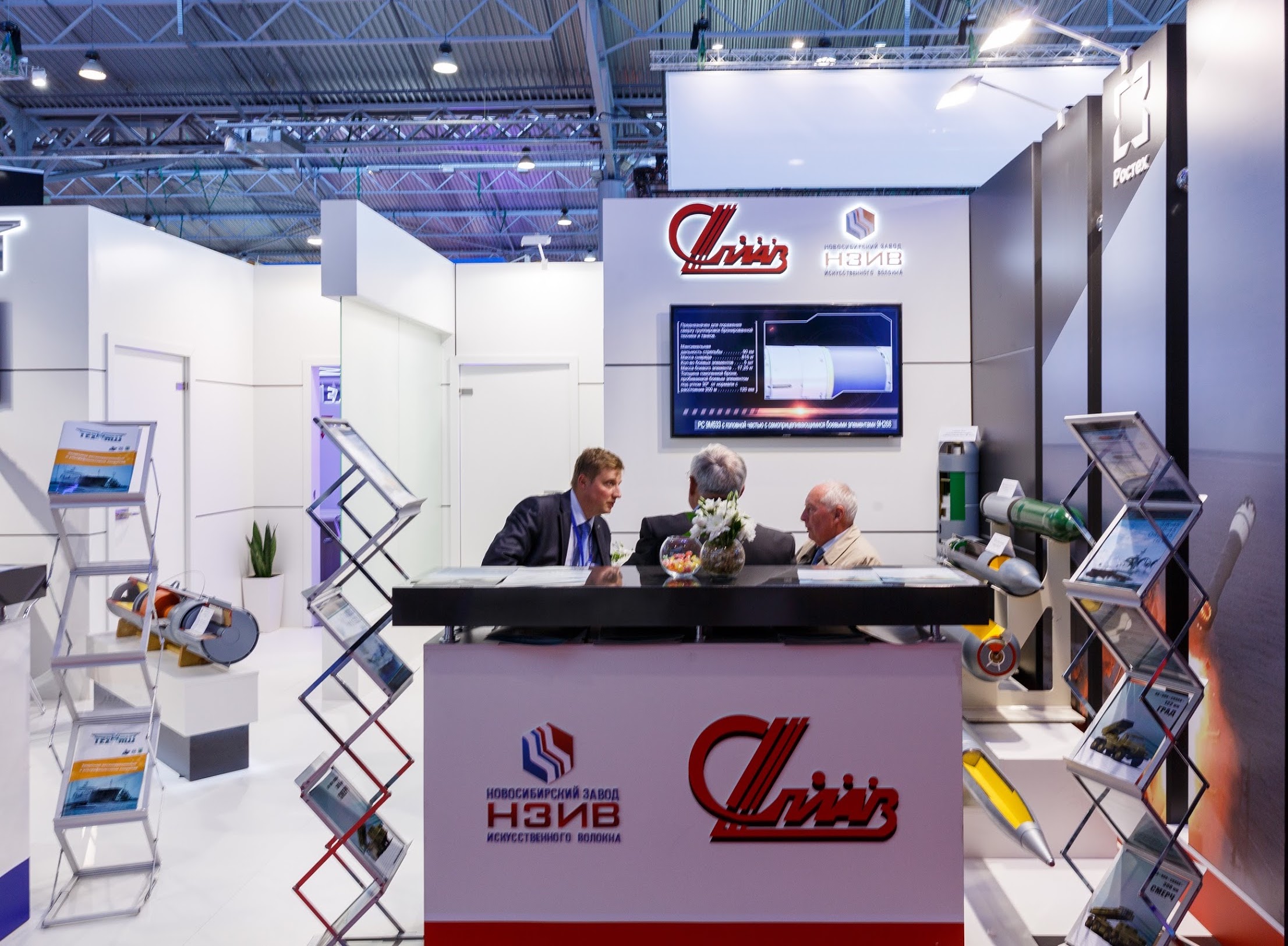
«Сплав» продемонстрирует на выставке «ЭкспоЭлектроника» гибкий печатный кабель
НПО «Сплав» им. А.Н. Ганичева Госкорпорации Ростех представит на Международной выставке электронных компонентов, модулей и комплектующих «ЭкспоЭлектроника-2022» гибкий печатный кабель – ГПК-МП.
Изделие не имеет отечественных и зарубежных аналогов. Основная его задача – снизить массу и габариты бортового электромонтажа.ГПК-МП обладает уникальными конструктивно-эксплуатационными характеристиками, стоек к термоударам, вакууму, радиации, незаменим в подвижном электромонтаже. Его применение позволяет расширить конструктивные возможности. Изделие выдерживает более 2 млн изгибов на радиус 15 мм, допускает изгиб с нелимитированным радиусом и возвратом в исходное состояние. Кроме использования в приборостроении может помочь в конструкторских решениях изделий арктического назначения, в криогенной энергетике, роботостроении и в снижении объемов и габаритов бортовых кабельных сетей большинства продуктов, где эти параметры критичны.
Минимальные температуры эксплуатации гибкого печатного кабеля –269 °С при фиксированном монтаже, –198 °С при подвижном монтаже, максимальная температура эксплуатации +300 °С в пределах наработки 1000 час, +600 °С кратковременно. Кабель не становится хрупким в жидком азоте. Продукция нашла применение как в оборонной, так и в гражданской промышленности.
24-я Международная выставка электронных компонентов, модулей и комплектующих ExpoElectronica 2022 проходит в МВЦ «Крокус Экспо» с 12–14 апреля 2022 года.
ExpoElectronica носит статус ведущей выставки электронной отрасли. На ней широко представлены электронные, полупроводниковые, электромеханические, пассивные компоненты, печатные платы и микросхемы, дисплеи, встраиваемые системы и многое другое.https://rostec.ru/news/splav-p...
Во Владикавказе запустили производство бескислородной меди
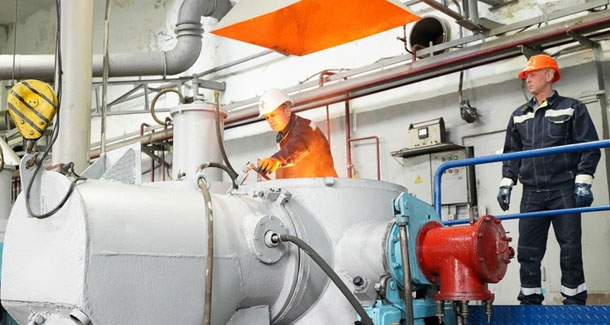
В Северной Осетии на владикавказском ОАО «Кристалл» состоялся официальный запуск модернизированного плавильного участка. Впервые после долгих лет простоя там начали производить востребованную на российском рынке продукцию — бескислородную вакуумно-плавленую медь.
После запуска плавильного цеха полноценное производство кристально чистой меди начнётся в мае. Пока работает только одна печь, здесь производят до трёх заготовок в смену — это около полутора тонн. А уже к концу года планируем запустить и остальные пять, увеличив объемы производства до 1200 тонн в год.
Раньше бескислородную вакуумно-плавленую медь экспортировали в Россию из Германии и Финляндии. Теперь её будут производить во Владикавказе. Для эффективной работы специалистам завода пришлось восстанавливать вакуумную систему печи. Модернизировали и часть управления. Сейчас оно электронное.
Такая медь, обладающая высокой прочностью, электропроводностью, большой устойчивостью к коррозии и другими характеристиками, в условиях западных санкций особенно востребована на российском рынке. Она широко применяется в электронной промышленности и на предприятиях ВПК. Чистая медь — лучшая замена серебру при производстве мобильных телефонов, компьютерных процессоров. Проблем с сырьем нет, его производят российские компании, УГМК и «Норникель». На «Кристалл» медь поступает в катоде.
«Одна тысячная примесей. Это как у золота: есть 585 проба и 999. То же самое у меди. Вот мы получаем сверхчистую медь, чище не бывает», — пояснил старший мастер плавильного участка Эдуард Джигкаев.
Завод «Кристалл» (впоследствии ОАО «Кристалл») был создан в 1963 году постановлениями ЦК КПСС и Совета Министров СССР. Предприятие производило продукцию из вакуумплавленных цветных металлов, сплавов высокой частоты и полуфабрикатов. Основной продукцией завода являлась вакуумплавленная медь марки MB.
Транссибирская магистраль: поезда пойдут быстрее
История Транссибирской магистрали.
Протяженность Транссибирской магистрали от Москвы до Владивостока составляет 8,3 тысячи километров. Сложнее всего было построить забайкальский участок Транссиба.
«Узким местом» стал Керакский тоннель на перегоне Ковали-Ульручьи. На карте:
https://yandex.ru/maps/?ll=124...
Ульручьи на карте Ковали - это похоже река Большие Ковали
https://yandex.ru/maps/?ll=124...
Старый двухпутный Керакский тоннель длиной 910 метров построен в 1910—1911 годах. За сутки через него проходит в среднем 80 пар поездов. Из-за серьезной загрузки и эксплуатации в сложных условиях тоннель уже не отвечает требованиям безопасности и пропускной способности.
В рамках национального проекта «Комплексный план модернизации и расширения магистральной инфраструктуры» планируется нарастить транзитный контейнеропоток в 4 раза и доставлять грузы из Азии в Европу за 7 суток. Для этого в прошлом году начали строить новый двухпутный Керакский тоннель. Он находится в 30 метрах от старого, который еще послужит в дренажных и эвакуационных целях.
В апреле 2022 года проходка верхней части нового тоннеля была выполнена на 70%. Работы идут круглосуточно, с двух сторон одновременно. Встреча проходческих бригад запланирована к осени 2022 года, после чего начнется внутренняя железобетонная отделка тоннеля.
Новый Керакский тоннель позволит увеличить скорость движения поездов и пропускную способность на забайкальском участке Транссиба.По федеральному проекту «Развитие железнодорожной инфраструктуры Восточного полигона железных дорог», входящего в нацпроект, идут мероприятия по модернизации железнодорожной инфраструктуры Байкало-Амурской и Транссибирской железнодорожных магистралей для увеличения транзитного контейнеропотока в 4 раза.
Строится самый длинный тоннель Забайкальской железной дороги
https://zen.yandex.ru/media/st...
Подготовительный этап производства на «ОДК-Кузнецов» стал цифровым
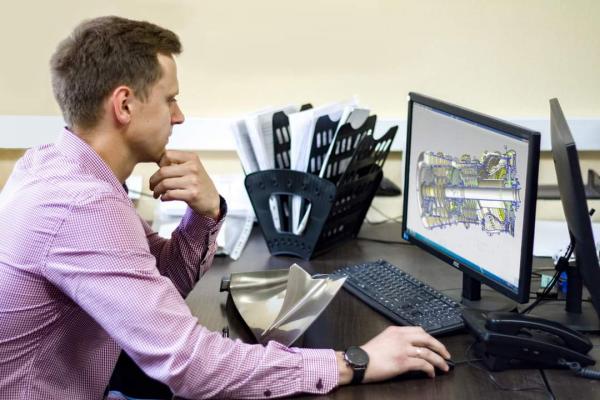
Самарское предприятие «ОДК-Кузнецов» Объединенной двигателестроительной корпорации внедрило цифровые технологии в подготовительный этап производства. Это позволит создавать и хранить всю технологическую документацию в электронном формате, а также упростит доступ к данным и сократит время обработки информации.
Цифровое решение, основанное на отечественном программном комплексе АСКОН, интегрировано в общую информационную архитектуру предприятия. Оно включает системы управления производством и бухгалтерского учета на базе «1С», системы разработки конструкторской документации для проектирования средств технологического оснащения и другие цифровые решения.
«Мы активно внедряем новые информационные технологии в производственный процесс. Завершилась цифровизация подготовительного этапа производства. На нем определяют наиболее эффективный способ, как воплотить задумку конструкторов в «железе». Цифровизация упростит доступ к информации и повысит эффективность рабочих процессов», – сообщил заместитель управляющего директора по развитию «ОДК-Кузнецов» Павел Бехер.
Специалисты предприятия уже прошли обучающие видеокурсы. Это позволило быстро и удобно познакомить специалистов с особенностями новых цифровых инструментов.
«Авиационное двигателестроение является на сегодня приоритетной отраслью в стратегии развития решений АСКОН для машиностроения, а предприятия Объединенной двигателестроительной корпорации – целевыми площадками для применения и совершенствования самых современных версий наших программных продуктов», – отметил руководитель дивизиона PLM АСКОН Иван Трохалин.
Россия создает уникальную авиационную технологию
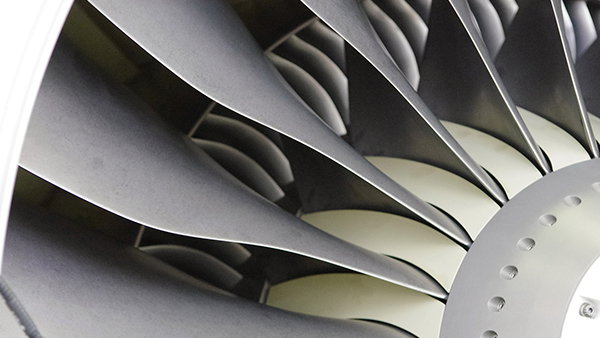
На фоне постоянных санкций против самых важных промышленных отраслей России наша страна внедряет собственные новейшие технологии. На этот раз речь идет о новом способе производства ключевой детали современных авиадвигателей. Что именно предложено нового и почему это критически важно для всей авиационной отрасли?
Объединенная двигателестроительная корпорация «Ростеха» сообщила, что на ее предприятиях освоена уникальная технология изготовления лопаток авиационных двигателей. В мире есть всего лишь шесть государств, которые имеют полные технологии проектирования и производства лопаток – и теперь Россия упрочила свое лидерство в этой отрасли. Чтобы объяснить исключительную важность этого события, придется углубиться в техническую часть вопроса.
Современный турбореактивный или турбовентиляторный двигатель невозможно представить без множества лопаток. Поднимаясь по трапу пассажирского самолета, мы видим их «частокол» в фронтальной проекции авиадвигателя – но это лишь первый ряд лопаток. Эта открытая невооруженному взгляду часть двигателя называется компрессор, и в ней происходит сжатие набегающего потока воздуха во время работы авиадвигателя.
Лопатки компрессора направляют набегающий поток, позволяя ему сжиматься максимально плавно. Это нужно для того, чтобы во входном канале компрессора не было ненужных и разрушительных скачков давления, а сам двигатель оказывал минимальное лобовое сопротивление. Именно для этих целей лопаткам придают сложную, изогнутую форму, максимально повторяющую направление набегающего потока, который заставляют пройти внутри авиадвигателя по сложной, сжимающиейся спирали.
Чтобы эта спираль и, как следствие, путь воздуха в компрессоре был максимально длинным, а рост давления – постепенным, компрессор делают многоступенчатым, выстраивая лопатки в десяток последовательных рядов. Поэтому, если разрезать турбореактивный или турбовентиляторный двигатель, внутри его мы увидим в основном два главных блока – компрессор и турбину, между которыми находится компактная камера сгорания.
В камере сгорания сжатый и нагретый воздух смешивается с авиационным керосином – и происходит горение топлива. Воздух резко нагревается, после чего попадает на второй лопаточный агрегат – турбину. На турбине часть энергии реактивной струи отбирают, тоже лопатками. Эта энергия позволяет вращать компрессор, обеспечивая сжатие новых порций воздуха.
Большая часть энергии нагретого воздуха уходит за пределы двигателя, создавая реактивную тягу, движущую самолет вперед. Турбину авиадвигателя тоже делают многоступенчатой, а лопатки в ней, опять-таки, имеют сложную криволинейную форму, чтобы обеспечить максимально плавное расширение реактивной струи.
При своей работе лопатки компрессора и турбины испытывают сильные и разнонаправленные механические воздействия: центробежные силы, сопротивление набегающего потока воздуха. Кроме того, лопатки турбины работают в условиях высоких температур – реактивная струя на первых ступенях турбины имеет температуру более 1000 ºС. Поэтому для материала лопаток нужен надежный, легкий и жаропрочный материал.
Как следствие, лопатка газотурбинного двигателя является одной из наиболее сложных и наукоемких в проектировании и изготовлении деталей авиадвигателя. При ее производстве используются редкие металлы и уникальные сплавы, а также композиционные материалы, гарантирующие легкость и прочность заготовки.
Алюминий, из которого состоит корпус самолета, для лопаток малопригоден, а жаропрочная сталь все же слишком тяжела. Идеальным материалом для лопатки является титан – легкий, прочный и жаростойкий металл. Из титана можно сделать даже композит: для этого в слитке можно создать двухфазный вариант титана, где одна из фаз будет отвечать за прочность и твердость наружного, поверхностного слоя лопатки, а внутренняя часть, с другой фазой, обеспечит общую гибкость детали.
Однако в обработке титана есть свои особенности. Поскольку лопатка имеет сложную, криволинейную форму, ее очень накладно изготавливать с помощью механической обработки. Ведь если ее вытачивать из цельной заготовки, то расход материала и инструмента будет просто непозволительным. Не так просто использовать и сварку – титан капризный материал при сварочных операциях, а любой сварочный шов в такой ответственной детали как лопатка будет слабым местом.
В итоге наиболее экономной и качественной технологией изготовления лопаток компрессора и турбины авиадвигателя в мире стала штамповка, когда профиль лопатки получается пластической деформацией исходной заготовки. В таком варианте механическая обработка минимальна и служит лишь для придания готовому изделию точных обводов, в основном созданных в результате штамповки. Нет и сварочных швов – лопатка представляет собой монолит, полученный из одной-единственной заготовки.
Штамповка титановых изделий – исключительно трудная технологическая операция. Многие титановые сплавы имеют очень узкое «температурное окно» для эффективной штамповки. Нагрел деталь выше нормы – будут утрачены свойства титанового композита, подал ее на пресс слишком холодной – штамповка внесет в структуру металла механические повреждения и разрывы. Кроме того, выбранная технология управляемого сгиба заготовки в готовую лопатку позволяет делать штамповку максимально «мягко», оставляя в готовой лопатке все преимущества двухфазного титанового композита.
Поэтому освоение в России технологии высокоточной штамповки титановых лопаток – это не просто небольшое технологические «улучшение», но целый пласт научных, конструкторских и производственных исследований, который позволил создать инновационный техпроцесс по самой ответственной и важной части любого авиадвигателя.
Описанные технологии теперь будут применяться Объединенной двигателестроительной корпорацией «Ростеха» при создании и производстве линейки гражданских авиадвигателей ПД-8 для самолета «Сухой Суперджет» SSJ-NEW, в двигателе ПД-14 для среднемагистрального лайнера МС-21 и в новой разработке – авиадвигателе ПД-35 для перспективных широкофюзеляжных дальнемагистральных самолетов.
Таким образом, существующие и перспективные российские самолеты смогут получить полную и разнообразную линейку отечественных авиадвигателей, которые будут находится по своему технологическому уровню либо наравне, либо даже выше лучших мировых образцов. Ведь использование композитного сплава на основе титана – это безусловный шаг вперед в конструкции авиадвигателя. Он обеспечивает меньший вес изделия, больший ресурс лопатки и, как следствие, более длительные межремонтные периоды и сниженную стоимость обслуживания.
Кроме того, технологические санкции, которыми сейчас пугают российский авиапром, становятся бесполезными. Снова и снова «Россия делает сама», показывая, что в нашей стране живет и развивается научная и производственная школа, работающая на самом переднем крае мировой научно-технической мысли.
Свежие комментарии